Boost for market development
Before the first regulatory step in 2009, it was generally known that the technical possibilities of motor efficiency had not yet been exhausted. Premium manufacturers were investing in the research and development of efficiency-enhanced motors, but were losing market share in Europe due to the advance of cheaper Chinese products. Reduced power consumption was not a high priority at the time for the main customer for electric motors, the mechanical engineering industry. This is because this industry is characterized by segmentation and specialization of production phases. This makes it very different from the electronics industries, for example, which is much more vertically integrated. Manufacturers and operators of the machines have different priorities; for both sides, a favorable procurement price was more important than long-term savings. It was therefore foreseeable that regulatory measures could provide a significant boost to efficiency development without overburdening the market.
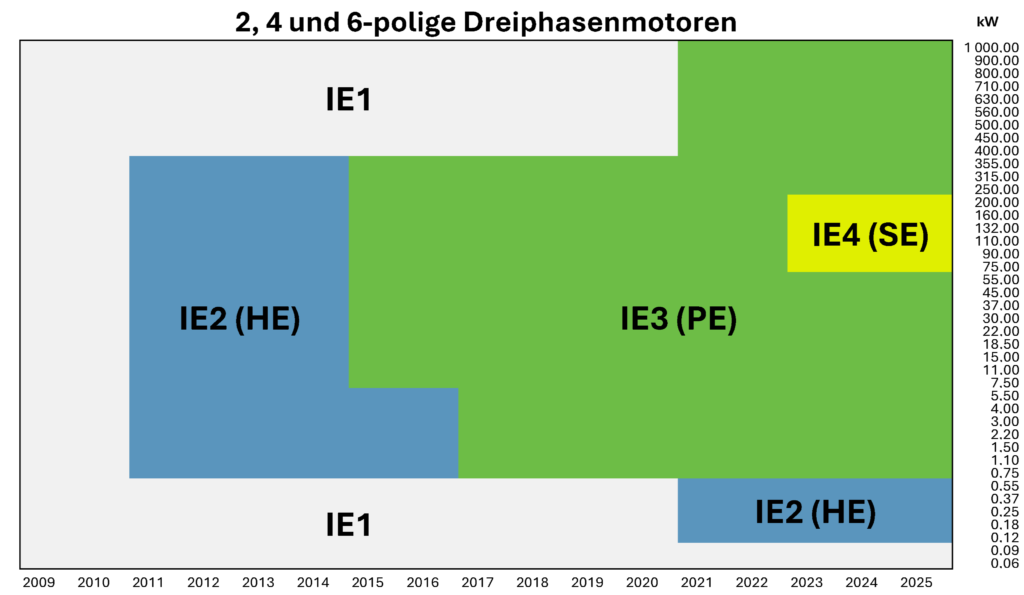
Sequence of the conversion steps
The IE1 class represents the minimum standard that was established on the market in the early 2000s. Its introduction replaced older regulations such as EFF1 and thus laid the foundation for the new classification. Measurement specifications were standardized without significantly raising the efficiency level. Instead, the measure served to prepare the industry for the upcoming changes and raise awareness of the importance of energy efficiency.
With the IE2 class, specific requirements for higher efficiency have already been set. This change was crucial to kick-start the development of more efficient motors and motivate the industry to use better technologies that reduce energy consumption. However, IE2 was not introduced for all motors, but only for standard three-phase motors with an output between 0.75 and under 400kW. This target zone was chosen because most of the energy consumed worldwide for electric motors drives precisely these motors. After 10 years, the scope was also extended to motors from 0.12kW and 12 years after its introduction to explosion-proof motors and 230V single-phase motors. These steps were taken when it became clear that IE2 efficiency could also be safely implemented in these technically more demanding areas of the electric motor spectrum.
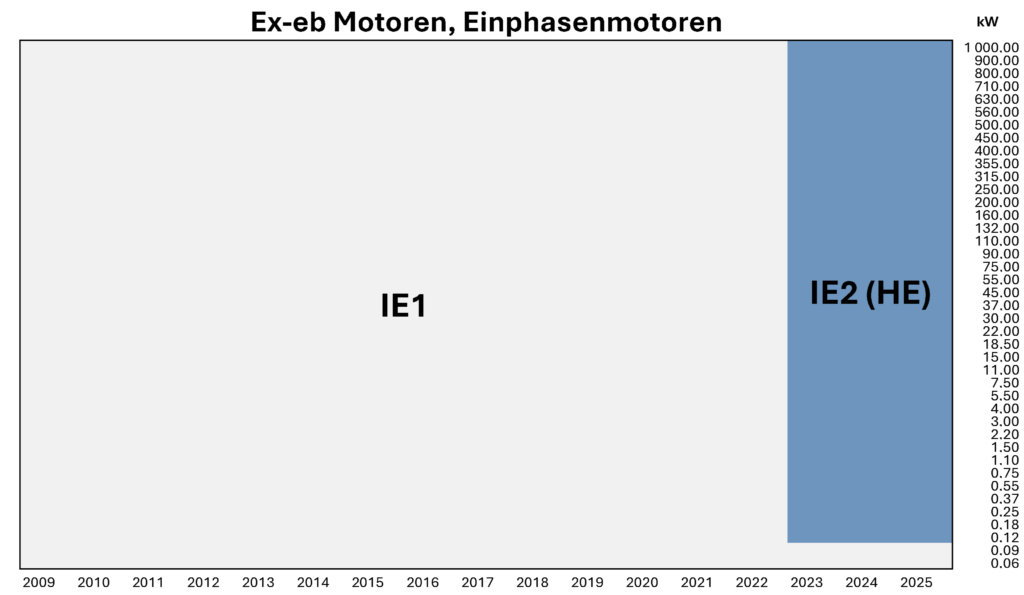
The IE3 and IE4 classes form the end point of motor-related regulation and set the benchmark for maximum energy efficiency in mains operation. They were introduced with a time lag, with various power ranges being gradually transferred to IE3 and IE4. Exceptions for 8-pole motors and brake motors were also removed with a time delay. Experts who were able to assess the technical feasibility were involved in this schedule, as higher efficiency can be achieved with varying degrees of ease for different motor sizes and speeds. In the range of 2, 4 and 6-pole motors between 75kW and 200kW, where the yield was easiest to increase, IE4 now applies, while IE3 is the efficiency class of choice in the neighboring ranges. The gradual penetration of all industrial systems with this technology will reduce the energy consumption of unregulated drives to a minimum.
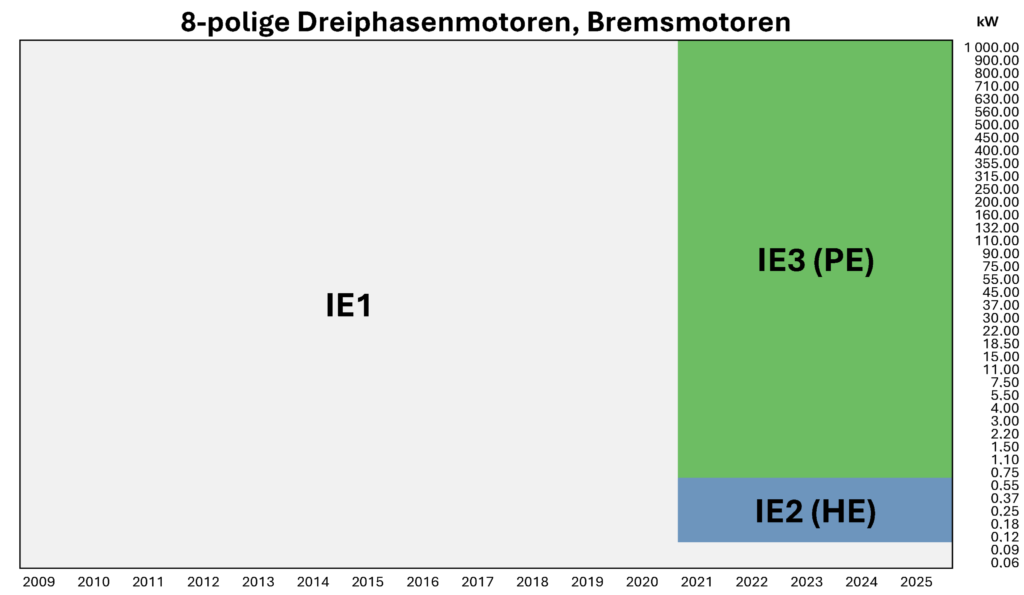
Further improvements with speed control
Power savings far above the level promised by the use of IE3 and IE4 motors can be achieved in applications without constant torque requirements. Switching the control of the motors to frequency inverters saves a lot of electrical energy, especially in the partial load range. However, in order to leverage these far greater savings potentials, production processes must be adapted, new technologies integrated and investments made in employee training. In order to successfully manage such a change, understanding and support from the management level are essential. Industrial companies with long-term thinking and decisive managers are pioneers in actively contributing to sustainability.